Представлен гоночный электромобиль с временем зарядки меньше 4 минут
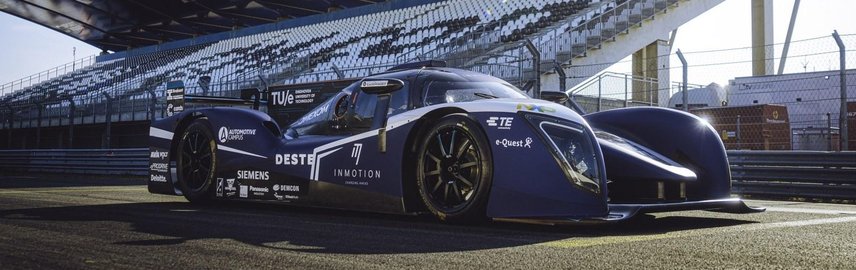
Сейчас зарядка Вашего электромобиля в лучшем случае занимает от 20 до 45 минут. Но вскоре Вы, возможно, сможете просто вернуться на дорогу, заплатив за кофе. Студенческая команда TU Eindhoven (TU / e) InMotion представила электрический гоночный автомобиль Revolution со временем зарядки всего 3 минуты 56 секунд от 10% до 80%. По праву это самый быстрозаряжаемый полностью электрический гоночный автомобиль в мире!
Техника
Аккумуляторная батарея имеет зарядную мощность 322 кВт, общую емкость 29,2 кВт*ч и запас хода 250 километров. За последние 2,5 года команде удалось сократить время зарядки на 66% – в прошлом году оно составило 12 минут. Насколько известно, это самый быстрозаряжаемый электромобиль для гонок на длинные дистанции в мире.
Сам аккумуляторный блок состоит из 8 аккумуляторных модулей, каждый из которых содержит 48 элементов (поставляется компанией Desten), что обеспечивает общее напряжение 806 В. Для быстрой зарядки этого аккумуляторного блока компания InMotion разработала собственную систему охлаждения на уровне элемента, состоящую из 2 отдельных контуров. Первый контур отводит тепло от аккумуляторных модулей путем пропускания жидкости, похожей на воду, через аккумуляторный блок. Второй контур состоит из системы охлаждения (подобной системе кондиционирования воздуха), которая используется для отвода тепла из первого контура и передачи его в окружающую среду. Преимущество такой системы охлаждения заключается в том, что она позволяет поддерживать оптимальную температуру аккумуляторов, даже если температура снаружи выше. Это позволяет заряжать от 10% до 80% за 4 минуты.
Чтобы продемонстрировать это быстрое время зарядки и по-настоящему протестировать аккумуляторную батарею на пределе ее возможностей, было принято решение установить аккумуляторную батарею в гоночный автомобиль LMP3. Шасси для этого автомобиля состоит из трех основных частей. Первым спереди является монокок, в котором находится ячейка безопасности для водителя. Эта деталь разработана и изготовлена Ginetta, производителем гоночных автомобилей из Великобритании. За монококом находится корпус аккумуляторной батареи, который является конструктивной частью автомобиля и изготовлен из углеродного композита. Этот корпус для аккумулятора разработан в сотрудничестве между Ginetta и InMotion и произведен компанией Ginetta. Наконец, за аккумуляторным блоком установлена трубчатая рама, которая соединяет переднюю часть автомобиля с задней подвеской и вмещает силовой агрегат. Эта трубчатая рама разработана компанией InMotion и изготовлена компанией CP-tech в Германии. Сама задняя подвеска основана на оригинальной задней подвеске шасси Ginetta. Однако внесены некоторые изменения, чтобы оптимально учесть разницу в весовом балансе нашего автомобиля по сравнению с оригинальным шасси Ginetta.
Силовой агрегат состоит из 3 основных компонентов: двух инверторов, двух двигателей и трансмиссии. Инверторы поставляются компанией Cascadia Motion и преобразуют постоянный ток от батарей в переменный ток для двигателей. Они также управляют двигателями и облегчают рекуперативное торможение; процесс восстановления тормозной энергии в аккумуляторной батарее. В Revolution установлено 2 двигателя от Phi Power, по одному подключенные к каждому заднему колесу. Двигатели вместе развивают максимальный крутящий момент 1040 Нм и пиковую мощность 324 кВт или 437 лошадиных сил. При массе электромобиля 1350 кг получается соотношение 323 л.с. на тонну. Между двигателями и колесами установлена трансмиссия фирмы Hewland Transmissions. Эта коробка передач имеет передаточное отношение 3:1.
Разгон с 0 до 100 км/ч менее чем за 4 секунды, при этом динамика после первой “сотни” не угасает: 100-200 км/ч за те же 4 секунды! А на автодроме La Sarthe удалось развить скорость 297 км/ч.
За связь болида с дорожным покрытием отвечают кольцевые слики Michelin Pilot Sport GT размерностью 30/65-18 спереди и 31-71-18 сзади.
За кулисами. Процесс создания рекордного электромобиля
Инженеры InMotion полностью внедрили цифровой дизайн корпуса и других важнейших компонентов Revolution. Команда в значительной степени полагается на пакет NX Teamcenter от Siemens. Команда из Эйндховена получает помощь от самой Siemens и ее партнера-консультанта Cards PLM Solutions. Самое замечательное в Teamcenter то, что вы можете разделить дизайн на подмодули, которые вы можете назначить одному человеку. Таким образом, вы все можете работать над дизайном одновременно, не мешая друг другу. При работе исключительно в NX каждому инженеру приходилось бы загружать дизайн целиком, чтобы повозиться со своей частью. При объединении всех изменений тратиться много времени и могут быть допущены ошибки. Весь дизайн болида Revolution находится в облаке, и каждый может легко разработать свою собственную часть. Как только изменения в этом модуле будут одобрены, они перейдут к полному дизайну, и каждый сможет снова получить к нему доступ.
3D-дизайн в NX Teamcenter статичен, но Inmotion может выполнять множество симуляций с его помощью.
"Можно приложить все виды усилий к элементам конструкции и посмотреть, как эти подсистемы реагируют на них", - объясняет инженер InMotion Коэн Джейкобс. Это часто приводит к большой головоломке, как в случае с трубчатой рамой, соединяющей заднее антикрыло, аккумуляторный отсек и трансмиссию. ’Мы часто моделировали это в FEM-пакете Siemens NX Nastran. Основываясь на исследованиях литературы и наших собственных знаниях по предыдущим автомобилям, мы подробно вводим силы и точки соприкосновения, чтобы увидеть, какова оптимальная конструкция. Это заняло довольно много итераций, в том числе потому, что мы варьировали используемый материал и потому, что точки подвеса несколько раз меняли положение в процессе разработки."
Команда InMotion также использует инструменты Siemens для достижения своей главной цели: сокращения времени зарядки..
Линн ван Моурик, менеджер по маркетингу InMotion: “Чем быстрее вы заряжаете аккумуляторы, тем выше ток и тем теплее становятся элементы. Тепло - самый большой враг аккумулятора “.
С помощью Star-CMM + студенты из Эйндховена смоделировали тепловой поток для охлаждения аккумулятора.
По другую сторону экрана находятся менеджер команды Джулия Нимейер и менеджер по партнерству Хике ван Хееш. У них был “довольно беспокойный год”. Королева Максима, министр Харберс и руководители крупнейших автопроизводителей; все выслушали историю компании InMotion, базирующейся в автомобильном кампусе в Хелмонде.

“Мы почти все живем в Эйндховене, но иногда таскали сюда матрасы и спальные мешки, чтобы работать всю ночь”, - говорит Ван Хееш. Это характеризует страсть команды из 30 человек. Например, поставка соединительной детали для системы охлаждения была отложена незадолго до важного срока в производственном процессе. “Мы услышали об этом в среду вечером, а в шесть часов утра следующего дня два члена команды были на пути в Соединенное Королевство, чтобы самим отправиться за деталями”.
Ключом к революционному времени зарядки является инновационная технология охлаждения. Когда аккумулятор заряжается быстро, выделяется много тепла. Нагрев вреден для аккумуляторов: он приводит к их деградации, и вы теряете запас хода. Студенческая команда предыдущих лет разработала инновационную технологию охлаждения на уровне аккумуляторных модулей, разместив охлаждающие пластины с охлаждающей жидкостью между модулями.
Чтобы еще лучше отводить тепло от аккумуляторной батареи, InMotion представила новый метод, который позволяет охлаждать их на клеточном уровне.

Нимейер: “Охлаждающая жидкость теперь течет между всеми элементами. Теперь мы можем охлаждать элементы по отдельности. Это обеспечивает длительный срок службы, а повторная быстрая зарядка таким образом больше не наносит вреда аккумулятору ”.
Команда провела несколько тестов, в ходе которых они заряжали автомобиль в гоночном темпе в течение 24 часов и не увидели никаких повреждений. Как именно работает система, команда держит в секрете.
Охлаждение на уровне элементов еще не распространено в электромобилях, поэтому InMotion также разработала свои собственные модули.
“Наша технология работает на уровне элементов. Между ячейками всего несколько миллиметров, поэтому мы действительно работали в очень малых масштабах ”, - сказал Нимейер. “Кроме того, было непросто интегрировать нашу систему в аккумуляторный отсек, который был разработан в предыдущие годы”, - добавляет Ван Хееш своему товарищу по команде. “У вас есть только один год, мы не можем изобретать все заново и сосредоточиться на том, где есть инновации”.
Подготовить все к презентации в том году было непростой задачей.
“На самом деле, по определению, вы ставите нереалистичные цели. Но, с другой стороны, вы также хотите чего-то достичь за один год. В этом году я ел в офисе чаще, чем дома, мы можем очень творчески готовить с помощью нашего утюга для сэндвичей ”, - смеется Ван Хееш.
В то время как нынешняя система разработана специально для гоночных автомобилей, студенты хотят упростить вождение на электротяге – и, следовательно, сделать его более доступным – для потребителей. Этим летом команда сделает автомобиль пригодным для езды и протестирует его на трассе. Результаты испытаний будут использованы следующей группой выпускников InMotion. Команда внедрила технологию в гоночный автомобиль LMP3.
Конечная цель?
“Участвуя в 24-часовой гонке в Ле-Мане, мы можем протестировать наш аккумулятор в самых сложных условиях. Именно поэтому мы уже внедрили нашу технологию в гоночный автомобиль LMP3, класс прототипов Ле-Мана ”, - ответил Нимейер.
“Это вызов, который не следует недооценивать. С технологической точки зрения это очень сложная концепция. InMotion продемонстрирует возможности электрической дозаправки, участвуя в 24 часах Ле-Мана в Garage 56 на электрическом гоночном автомобиле с быстрой зарядкой на выносливость”, - InMotion
Источники: